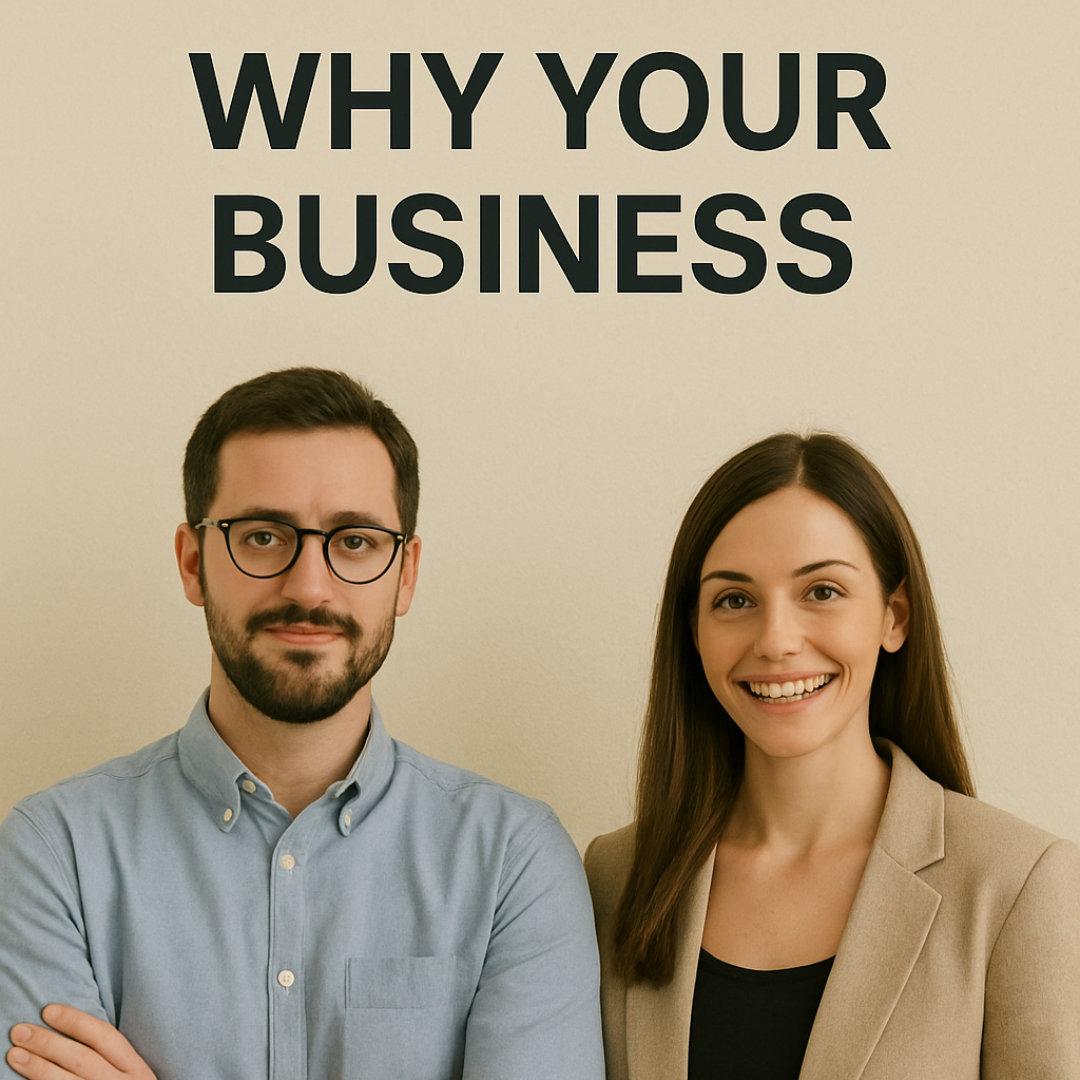
Introduction:
If you think Lean and Six Sigma are only for factories or Fortune 500 companies, think
again. Whether you’re a nonprofit stretched thin on staff or a small business trying to do
more with less, the principles of Lean thinking can help you cut waste, boost efficiency, and
serve your customers or community better.
What Is Lean Thinking (In Simple Terms)?
Lean is about one thing: getting more value with less waste. It’s a mindset and a set of tools
that help you find inefficiencies, streamline your processes, and improve what really
matters. When paired with Six Sigma—a method for reducing errors and variation—you get
a powerful combo for consistent, high-quality results.
5 Places Small Teams Waste Time Without Realizing It:
1. Redundant Meetings – Too many check-ins and unclear agendas slow down momentum.
2. Manual Processes – Spreadsheets and paper forms that could be automated.
3. Misaligned Roles – When responsibilities aren’t clear, tasks fall through the cracks.
4. Lack of SOPs – Without standard operating procedures, every task feels like reinventing
the wheel.
5. The “We’ve Always Done It This Way Trap – Tradition isn’t always efficient.
Real-World Example:
At Clear Route Consulting, we worked with a community nonprofit that was struggling with
donor acknowledgment delays. By mapping the process, we found three unnecessary
handoffs and reduced their response time by 60%. They didn’t need more staff—they
needed smarter systems.
Why Lean Works for Community-Driven Organizations Too:
– It improves communication and accountability
– It frees up resources for mission-critical work
– It helps secure funding by showing impact and efficiency
– It boosts morale because teams finally feel in control
Ready to Get Started?
You don’t need to be a Six Sigma Black Belt to apply Lean thinking. Start with a small
process that frustrates your team, map it out, and look for waste. Or better yet, let us guide
you.
Download our free Hoshin Planning Template or schedule a consultation with Clear Route
Consulting. Let’s make operational excellence your new normal.
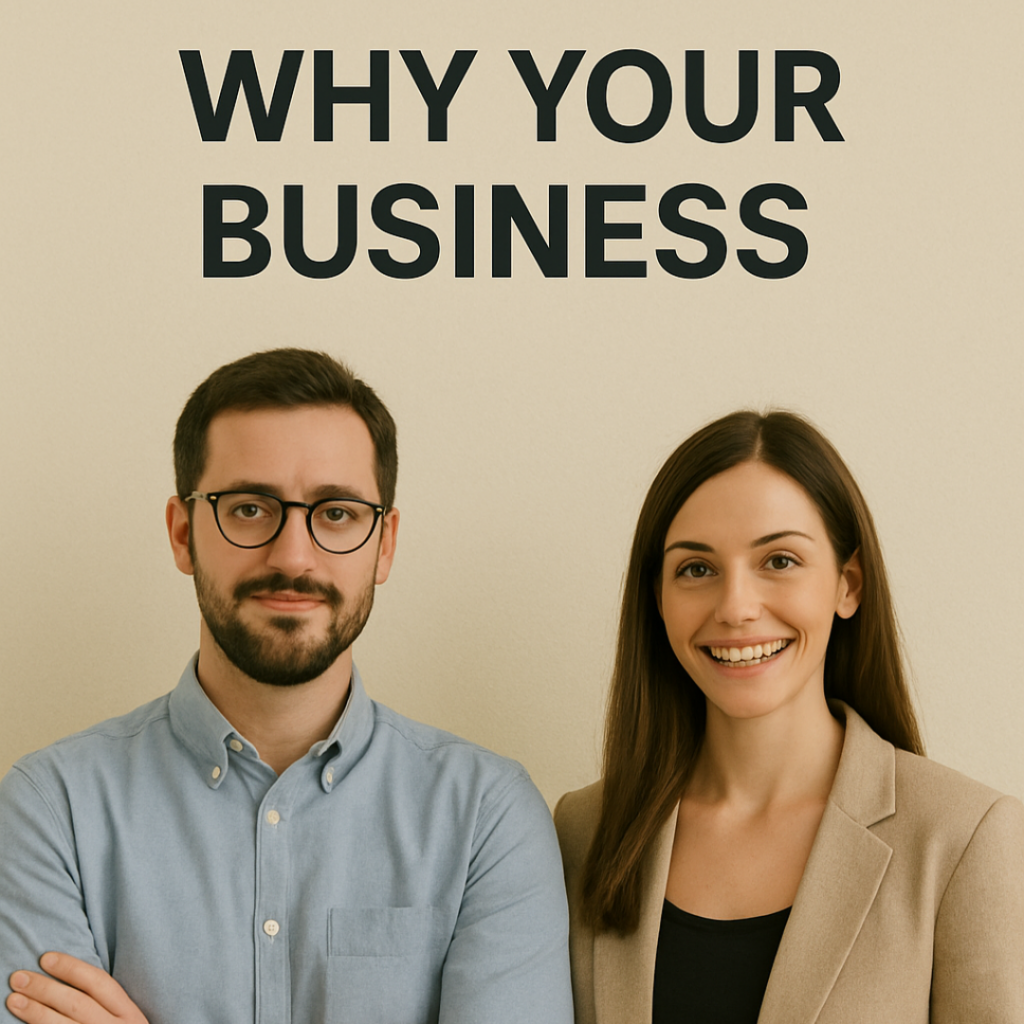
Introduction:
If you think Lean and Six Sigma are only for factories or Fortune 500 companies, think
again. Whether you’re a nonprofit stretched thin on staff or a small business trying to do
more with less, the principles of Lean thinking can help you cut waste, boost efficiency, and
serve your customers or community better.
What Is Lean Thinking (In Simple Terms)?
Lean is about one thing: getting more value with less waste. It’s a mindset and a set of tools
that help you find inefficiencies, streamline your processes, and improve what really
matters. When paired with Six Sigma—a method for reducing errors and variation—you get
a powerful combo for consistent, high-quality results.
5 Places Small Teams Waste Time Without Realizing It:
1. Redundant Meetings – Too many check-ins and unclear agendas slow down momentum.
2. Manual Processes – Spreadsheets and paper forms that could be automated.
3. Misaligned Roles – When responsibilities aren’t clear, tasks fall through the cracks.
4. Lack of SOPs – Without standard operating procedures, every task feels like reinventing
the wheel.
5. The “We’ve Always Done It This Way Trap – Tradition isn’t always efficient.
Real-World Example:
At Clear Route Consulting, we worked with a community nonprofit that was struggling with
donor acknowledgment delays. By mapping the process, we found three unnecessary
handoffs and reduced their response time by 60%. They didn’t need more staff—they
needed smarter systems.
Why Lean Works for Community-Driven Organizations Too:
– It improves communication and accountability
– It frees up resources for mission-critical work
– It helps secure funding by showing impact and efficiency
– It boosts morale because teams finally feel in control
Ready to Get Started?
You don’t need to be a Six Sigma Black Belt to apply Lean thinking. Start with a small
process that frustrates your team, map it out, and look for waste. Or better yet, let us guide
you.
Download our free Hoshin Planning Template or schedule a consultation with Clear Route
Consulting. Let’s make operational excellence your new normal.